سخت کاری فلزات چیست؟
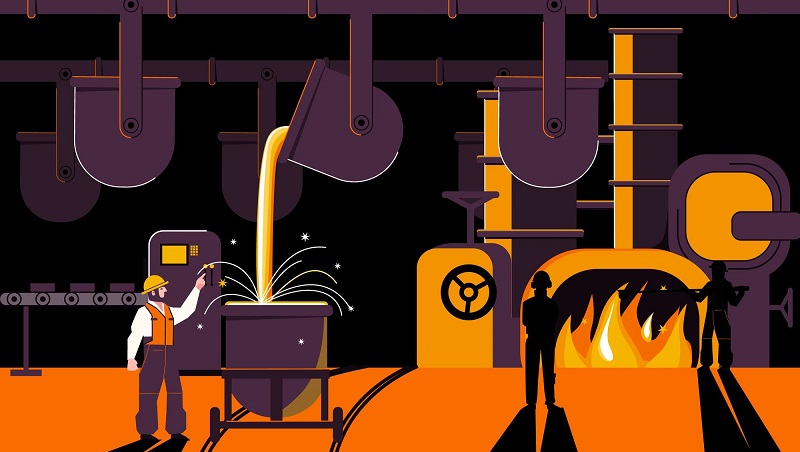
در دنیای امروز، فلزات به بخش مهم و جدایی ناپذیری از انواع مختلف صنایع تبدیل شدهاند. به همین دلیل نیز بسیاری از فرآیندها بر روی فلزات انجام میشود، که خواص فیزیکی آنها مانند استحکام یا ماندگاری در محیط را افزایش میدهد. بدیهی است که بخش بیرونی فلزات به استحکام و مقاومت بیشتری در برابر عواملی هچون سایش احتیاج دارد.
سخت کاری فلزات نیز یکی از روشهایی است که دارای انواع مختلفی است و میتواند برخی از ویژگیها مانند سازگاری با شرایط مختلف آب و هوایی را در فلزات تقویت کند. در واقع در روند ساخت فلزات کاربردی بعد از مرحله استخراج آهن، مرحله سخت کاری فلزات آغاز می شود که به وسیله آن می توان آهن را به شکلی که به آن نیاز داریم در بیاوریم. در این مقاله در ابتدا به بررسی مفهومهای مرتبط با سخت کاری میپردازیم و در ادامه سخت کاری و انواع مختلف آن را بررسی میکنیم.
فلزکاری چیست؟
به طور کلی به فرآیندهای مختلفی که در آنها فلزات شکلهای مختلف میگیرند، فلزکاری گفته میشود. این فرآیندها که معمولاً به سه نوع شکل دهی، برش و اتصال دیده میشوند. فلزات را برای اجرای کارهای مختلفی مانند ساخت ابزار آلات، قطعات یا سازهها آماده میکنند. فلزات آهنی و غیر آهنی مختلفی در این فرآیندها استفاده میشوند که میتوان از انواع آنها به فولاد، آلومینیوم، طلا، نقره، برنز، آهن و… اشاره کرد.
به علاوه برخی از رایجترین روشهای فلزکاری شامل برش کاری، جوش کاری، ریختهگری و قالبگیری هستند.
جالب است بدانید که اساس فلزکاری به طور کلی بر این مسأله استوار است که خواص فلزات تحت اثر ساختار اتمی و ساختار میکروسکوپی فلزات میتواند تغییر کند. بنابراین در زمانی که نسبت اجزای میکروسکوپی ماده را با استفاده از فلزکاری تغییر میدهیم، خواص مکانیکی آن نیز تحت تأثیر قرار میگیرد.
عملیات حرارتی چیست؟
به طور کلی عملیات حرارتی عملیاتی است که در طی آن با افزایش دمای یک فلز و نگه داشتن آن و سپس سرد کردن سریع آن میتوان، برخی از خواص مکانیکی را تغییر داد یا بهبود بخشید. عملیات حرارتی به طور معمول برای تغییر استحکام، دوام، شکلپذیری یا برخی از خواص مکانیکی دیگر مورد استفاده قرار میگیرد. آن چه در مورد عملیات حرارتی اهمیت دارد این است که تمام مراحل این عملیات در فاز جامد انجام میشود.
هدف از اجرای عملیات حرارتی چیست؟
عملیات حرارتی را میتوان با هدفهای مختلفی انجام داد. برخی از این هدفها شامل موارد زیر هستند.
- بهبود شکلپذیری
- آزادسازی تنشهای داخلی
- اصلاح اندازه ذرات تشکیل دهنده
- افزایش سختی و استحکام
به علاوه از روشهای مختلف عملیاتهای حرارتی میتوان، برای بهبود خواص مغناطیسی، هدایت الکتریکی و تبلور مجدد ساختار فلرات سخت کاری شده نیز استفاده کرد. در واقع استفاده کردن از این فلزات در ساختمان سازی بسیار ایمن تر خواهد بود مخصوصا اگر در کنار آن از بتن مسلح نیز استفاده کنید.
عملیاتهای حرارتی مختلف شامل چه مواردی هستند؟
برخی از انواع رایج عملیاتهای حرارتی سخت کاری، بازپخت، برگشت دادن (تمپرینگ)، سخت کاری پوسته (سطح) و نرماله کردن هستند که سخت کاری بیش از همه مورد استفاده قرار میگیرد.
سخت کاری فلزات چیست؟
سخت کاری فلزات یکی از رایجترین عملیاتهای حرارتی است که بر روی فلزات انجام میشود تا خواص مکانیکی فلزات بهبود پیدا کند و فلزات از دوام و استحکام بالاتری برخوردار شوند. به عبارت دیگر سخت کاری فلزات یکی از روشهای فلزکاری متالورژی است که با انجام شدن آن، سختی فلزات در برابر وارد شدن فشار و ضربات افزایش پیدا میکند. با افزایش طول عمر و کاهش درصد آسیب دیدگی در طول زمان همراه است که باعث میشود بتوان به طور مؤثرتری از فلزات در صنایع مختلف استفاده کرد. برای مثال برخی از قطعات مانند میل لنگ، میل بادامک، چرخدنده و… نیاز به مقاومت بالا در برابر ضربه وسایش دارند که با سخت کاری فولاد میتوان این ویژگیها را ایجاد کرد.
سخت کاری فلزات چگونه انجام میشود؟
به طور کلی سخت کاری فلزات در طی سه مرحله اصلی انجام میشود که این مراحل را در ابتدا برای شما ذکر کردهایم.
حرارت دهی
در این مرحله به ماده دمایی بالاتر از دمای بحرانی داده میشود تا رسوبات غنی از عناصر حل شونده حل شوند. جالب است بدانید که دمایی که در این مرحله به فلزات داده میشود تقریباً نزدیک به دمای تغییر فاز است. با ایجاد این دما یک محلول جامد تشکیل میشود و ساختار میکروسکوپی ماده مورد نظر شروع به تغییر میکند.
در این مرحله میتوان تغییر شکل مورد نظر را ایجاد کرد و در قدم بعدی با کاهش اصولی دما ماده بهبود یافته را به حالت اول بازگرداند. از پرکاربردترین تجهیزاتی که برای این مزجله مورد استفاده قرار میگیرند، میتوان به کورههای گازی و القایی اشاره کرد.
نگهداری دما یا حفظ دما
در این مرحله باید از ثابت ماندن دما در حین تغییر ریز ساختار مواد اطمینان حاصل کنید. به این فرآیند نگهداری یا اصطلاحاً خیساندن میگویند. برای روشهای مختلف سخت کاری باید مدت زمانهای مختلفی برای این مرحله در نظر گرفت. به طور کلی اپراتور تمام قسمتهای قطعه فلز مورد نظر را بررسی میکند تا مطئن شود که دارای دمای مورد نظر هستند.
خنک کاری
در این مرحله دما سریعاً کاهش پیدا میکند. این کاهش دما میتواند با استفاده از قرار دادن قطعه مورد نظر در معرض آب، آب نمک (سدیم کلرید)، روغن، نیتروژن مایع و یا هوا انجام شود. پس از انجام مرحله سخت کاری ممکن است شکل فلز به حالت اولیه برگردد یا برای همیشه تغییر کند.
مطلب پیشنهادی: ضریب نفوذ پذیری خاک چیست؟
تفاوت انواع دماها
دمای نرماله کردن
دمای نرماله کردن یا دمای سخت کاری به دمایی گفته میشود که در آن ریز ساختار ماده شروع به یکنواخت و منظم شدن میکند. این دما برای فلزات مختلف متفاوت است. برای مثال برای فولاد این دما برابر با ۸۱۵ تا ۹۸۰ درجه سانتی گراد است.
دمای بحرانی
دمای بحرانی به دمایی گفته میشود که در آن ساختار بلوری ماده شروع به تغییر میکند و دارای دو زیر مجموعه دمای بحرانی بالایی و پایینی است.
دمای بحرانی بالایی
این دما در واقع به دمایی گفته میشود که کاهش آن باعث شروع تبلور مجدد ماده و بازگشت آن به حالت اولیه میشود. در صورتی که مادهای در دمای نرماله کردن خود قرار داشته باشد با کاهش دما در دمای بحرانی بالایی قرار میگیرد. برای مثال دمای بحرانی بالایی برای فولاد با توجه به محتوای کربن میتواند بین ۷۲۳ تا ۹۱۰ درجه متغیر باشد.
دمای بحرانی پایینی
این دما در واقع نشان دهنده دمایی است که در دماهای کاهش یافتهتر از آن ریز ساختارهای تشکیل شده در دمای نرماله دیگر وجود نخواهند داشت. برای مثال دمای بحرانی پایینی برای فولاد برابر با ۷۲۳ درجه است. به طور کلی مرحله نگهداری یا حفظ دما با توجه به دمای نرماله کردن و دماهای بحرانی بالایی و پایینی انجام میشود.
سخت کاری فلزات به چند روش انجام میشود؟
سخت کاری فلزات دارای انواع مختلفی است که هر کدام از آنها میتوانند ویژگیهای خاصی را در فلز مورد نظر تقویت کنند و بهبود ببخشند. برخی از روشهای محبوب سخت کاری فلزات شامل موارد زیر هستند:
روش کوئنچینگ یا آبدهی در دو رسانه (Quenching)
در این روش از افزایش دما و سپس کاهش دمای ناگهانی استفاده میشود. برای انجام این روش ابتدا دمای فلز مورد نظر را با استفاده از منابع گرمایی مختلف مانند کورههای القایی یا شعله گاز نیتروژنی تا رسیدن به دمای تبلور بالا میبرند. در قدم بعدی با استفاده از یک یا دو رسانه خنککننده مانند آب نمک، روغن و یا هوا دما را به طور ناگهانی کاهش میدهند. در طی انجام این پروسه ریز ساختارهایی با نام مارتنزیت در فلزشکل میگیرد که دارای استحکام بسیار بالایی است و مقاوت فلز را در برابر سایش و ضربه بسیار افزایش میدهد.
روش نیتریده کردن (Nitriding)
در طی این روش فلزات را تا دماهای بسیار بالا گرم میکنند و سپس در معرض مواد نیتروژن دار یا آمونیاک قرار میدهند. این کار باعث میشود ذرات نیترید در فلز به وجود بیایند که دارای استحکام بالایی در برابر ضربه و سایش هستند. لازم است به این نکته توجه شود که برای انجام این پروسه به ذرات سازنده نیترید مانند کروم یا مولیبدن بر روی فلز نیاز داریم. روش نیتریده کردن در مقایسه با روش آبدهی در دو رسانه به گرمای کمتری احتیاج دارد و این باعث میشود بتوان آن را راحتتر انجام داد.
روش کربنیزه کردن (Carbonizing)
این روش یکی از روشهای رایج سخت کاری است که به خصوص درباره فولاد از آن استفاده میشود. در این روش یک آلیاژ فولادی تا دماهای بالا گرم میشود و سپس در معرض کربن قرار میگیرد. در این روش میتوان از انواع جامد، مایع یا کاز کربن استفاده کرد. در نهایت در این روش ذرات کاربید به وجود میآیند که باعث افزایش استحکام در فلز مورد نظر خواهند شد. این روش نیز به گرمای بسیار بالایی احتیاج ندارد که جزء مزیتهای آن به حساب میآید.
روش سلف تمپرینگ (Self-tempering)
در این روش قطههای فولادی پس از عبور از دستگاههای خنککننده و بدون نیاز به هیچ گرمایش دوبارهای از طریق گرمای موجود در خود فلز سخت کاری میشوند. در واقع در طی این پروسه دمای هسته فلز از دمای سطح بیشتر است و این مسأله باعث جریان پیدا کردن گرما از هسته به اطراف میشود که باعث ایجاد ساختارهای مارتنزیتی و افزایش استحکام فلز میشود.
فرایند تشکیل مارتنزیت که همراه با خنک شدن آغاز میشود، در مرحله بعدی سختکاری در دماهای ۲۰۰، ۳۰۰، ۴۰۰ و ۵۰۰ درجه سانتیگراد با تشکیل مخلوط فریت-کاربید همراه خواهد بود. آزمایشها نشان میدهند که دمای ۵۶۰-۵۰۰ درجه سانتیگراد برای انجام فرایند سلف تمپرینگ بسیار مناسب است.
روش مارتمپرینگ (Martempering)
در این روش فلزات به صورت سریع و پله پله خنک میشوند. در طی این روش در مرجله اول فولاد را در دمای بالاتر از دمای بحرانی آن قرار میدهند و سپس در دمای ۱۵۰ الی ۳۰۰ درجه سانتی گراد و در حمام نمک مذاب نگهداری میکنند.
در مرحله بعدی فلز در دمای بالاتر از دمای بحرانی نگهداری میشود، تا امکان یکسانسازی دما و خنکسازی در هوا یا روغن ایجاد شود. در نهایت فولاد مورد نظر با استفاده از روشهای مختلف متعادل میشود و با استفاده از خنکسازی پلهای آستنسیت به مارتنزیت تبدیل میشود.
عملیات سخت کاری فولاد چگونه انجام میشود؟
فولاد یکی از پر مصرفترین آلیاژها است که از ترکیب آهن و کربن ساخته میشود و در صنایع مختلفی کاربرد دارد.
سخت کاری فولاد نیز مانند دیگر فلزات دارای ۳ مرحله مشخص حرارت دهی، نگهداری یا حفظ دما و خنک کاری است.
دمای سخت کاری و مدت زمان نگهداری برای فولاد به خواص فیزیکی و شیمیایی آن بستگی دارد. پس از آن که فولاد تحت حرارت قرار میگیرد محلول جامد که همان آستنیت است، به مادهای با ساختار میکروسکوپی سخت که به آن مارتنزیت گفته میشود، تبدیل میشود. سخت کاری فولاد میتواند باعث تغییر و بهبود بسیاری از خواص فولاد شود. برخی از رایجترین این تغییرات شامل موارد زیر هستند.
- بهبود خاصیت چکش خواری
- بهبود قابلیت ماشین کاری
- بهبود خواص مغناطیسی و الکتریکی
- افزایش مقاومت در برابر ضربه و سایش
- از بین بردن تنشهای باقی مانده
- بهبود ریز ساختار ماده
- افزایش جذب انرژی
- بهبود خواص برش
مطلب پیشنهادی: فشار استاتیک چیست؟
سمنتیت چیست؟
سمنتیت که با عنوان کاربید آهن نیز شناخته میشود، یک ترکیب شیمیایی از آهن و کربن است که در اغلب آلیاژهای آهن مانند فولاد یافت میشود. یکی از ویژگیهای بارز این ماده سختی و شکنندگی آن است. به علاوه سمنتیت از نظر ترمودینامیکی یک ماده کاملاً ناپایدار است که با اعمال حرارت کافی، میتوان آن را به آستنیت یا گرافیت تبدیل کرد.
آستنیت چیست؟
در مرحله حرارت دهی به آلیاژهای آهن در دماهای بین ۷۵۰ تا ۱۴۵۰ درجه سانتی گراد، یک محلول جامد با نام آستنیت ایجاد میشود. در واقع در طی عملیات سخت کاری زمانی که ریز ساختارهای آلیاژ مورد نظر به طور کامل آستنیت تبدیل میشود و میزان کربن موجود در آن ثابت میشود، مراحل بعدی سخت کاری آغاز میشوند.
مارتنزیت چیست؟
پس از آن که محلول جامد آهن و کربن را در مرحله سردسازی قرار میدهند، یک ساختار بلوری بسیار سخت تشکیل میشود که به آن مارتنزیت گفته میشود. در واقع در طی فرآیند سخت کاری فولاد کربن موجود در ساختار آستنیت به دلیل تعداد اتمها نمیتواند، فرصت پراکندگی و خروج از ساختار بلوری آلیاژ را پیدا کند.
عملیات حرارتی سخت کاری سطحی چیست و چگونه انجام میشود؟
این روش که به آن سخت کاری پوستهای نیز گفته میشود، همان طور که از نام آن مشخص است برای سخت کاری سطح بیرونی فلزات استفاده میشود. به طور کلی در طی این عملیات یک لایه نازک بر روی فلز ایجاد میشود و باعث افزایش سختی و مقاومت سطح بیرونی فلز میشود.
برای این کار معمولاً مراحل افزایش دما، تغییر ساختار بلوری فلز و اضافه کردن عناصر جدید به سطح فلز باید طی شوند.
جالب است بدانید که این فرآیند شکلپذیری و قابلیت ماشین کاری قطعات فلزی را کاهش میدهد. به همین دلیل نیز معمولاً ابتدا مراحل دیگر انجام میشود و سپس قطعات نهایی برای سخت کاری سطحی آماده میشوند.
سخت کاری شعلهای
در این روش با استفاده از سوخت گازهای قابل احتراقی مانند گاز طبیعی لایه نازکی از سطح قطعه مورد نظر را حرارت میدهند تا به دمای بحرانی برسد و سپس آن را خنک میکنند. این روش معمولاً برای کل آلیاژ استفاده نمیشود و فقط برای بخشهای مشخصی انجام میشود. این کار باعث میشود خاصیت مواد فقط در همان نقطه خاص تغییر کند.
در این روش نیز سطح بیرونی قطعه مورد نظر سخت کاری میشود و درون فلز نرم باقی خواهد ماند. انجام این روش بر روی فلزات دارای مزایایی مانند افزایش عمر خستگی قطعه و استحکام مقاومت خمشی و پیچشی است. برخی از رایجترین مواردی که در آنها از این روش استفاده میشود شامل ساخت انواع غلتکها، قالبهای بزرگ، قالبهای صنعتی، چرخ دندههای صنعتی و لبه تیز چاقوها هستند.
پیرسختی یا سخت کاری رسوبی چیست؟
پیرسختی یکی از روشهای سخت کاری فلزات است که برای بهبود خواصی مانند استحکام قطعه مورد نظر استفاده میشود. در طی این پروسه یک فاز جدید در ماده به وجود میآید. این فاز شامل ذرات ریز و یکنواخت جامد است که در زمینه فاز اصلی تشکیل میشود و در نهایت ته نشینی ذرات جامد یا رسوبات باعث بهبود خواص مکانیکی فلز میشود.
به طور کلی از پیرسختی برای بهبود استحکام فلزات استفاده میشود و تحت این فرآیند میتوان از آلیاژهایی مانند تیتانیوم و آلومینیوم که در حالت عادی دارای استحکام کافی نیستند، در مواردی که به استحکام نیاز دارند استفاده کرد.
مراحل ایجاد پیر سختی
برای انجام پیر سختی باید سهمرحله زیر را طی کرد:
بازپخت محلول
در این مرحله به روش بازپخت محلول به آلیاژهای مورد نظر گرما داده میشود. در این مرحله فلز مورد نظر به همراه یک محلول جامد فلزی مانند مس در معرض افزایش حرارت قرار میگیرد و دما تا زیر نقطه یوتکتیک افزایش مییابد.
در این دما تمامی ذرات فلز به صورت همزمان شروع به کریستال شدن میکنند. در طی این فرآیند محلول جامد در فلز اصلی ته نشین میشود و یک ترکیب میان فلزی ایجاد میشود. در طی این روش پیوندهای فلزی به کوولانسی تغییر میکنند و ساختار غیر همگن ماده به ساختار همگن تبدیل میشود. در طی این مرحله نگه داری ترکیب در دمای مناسب از اهمیت زیادی برخوردار است و دما در صورتی که کم باشد میتواند، بازپخت را بیاثر کند و زیاد بودن دما باعث ذوب مواد میشود.
کوئنچینگ
در این مرحله باید محلول را سرد کنید. سردسازی سریع باعث میشود، مواد حل شده توانایی خروج نداشته باشند.
پس از انجام این مرحله آلیاژ در حالت شبه پایدار، فوق اشباع و تک فازی قرار میگیرد. متداولترین موادی که در این مرحله برای سرد کاری از آنها استفاده میشود شامل آب و روغن و گاز هستند.
پیرسازی
مرحله پیرسازی آخرین و زمان برترین مرحله در انجام پیر سختی است. در این مرحله ماده در معرض یک دمای متوسط قرار میگیرد و در این دما ثابت میماند. دمای دقیق مورد نیاز در پیرسازی به ترکیب ماده بستگی دارد. با گذشت زمان محلول اشباع به یک آلیاژ دو فازی تبدیل میشود. از پیرسختی برای موادی مانند آلیاژهای آلومینیوم، منیزیوم، نیکل، تیتانیوم، فولاد ضد زنگ و برخی از انواع فولاد استفاده میشود.
آنیلینگ یا بازپخت چیست؟
بازپخت یکی دیگر از انواع روشهای حرارتی است که برای افزایش خاصیت نرمی، شکلپذیری و کاهش سختی آلیاژها از آن استفاده میشود. بازپخت دارای کاربردهای مختلفی است. برخی از این کاربردها شامل موارد زیر هستند:
- بهبود خاصیت نرمی و شکلپذیری ماده برای انجام عملیاتهای خم کاری یا پرس کاری
- بهبود خواص ماشین کاری برای جلوگیری از سایش ابزارآلات
- آزاد شدن تنشهای پسماند برای کاهش احتمال ترکخوردگی و مشکلات حین ماشینکاری
این مطلب را از دست ندهید: دسته بندی عنصرها
بازپخت چگونه انجام میشود؟
برای انجام بازپخت بر روی فلزات و آلیاژهای مختلف باید موارد زیر را انجام داد.
بازیابی
در این مرحله با منابع مختلف گرمایی مانند کوره دمای فلز افزایش داده میشود تا به نقطه رهاسازی تنش برسد.
تبلور مجدد
در این مرحله دمای ماده باید به بالاتر از دمای تبلور مجدد و پایینتر از دمای ذوب برسد. در این مرحله بدون نیاز به اعمال تنشهای اولیه دانههای جدید در ساختار ماده تشکیل میشود.
رشد دانه
در این مرحله دانههای جدید رشد میکنند و رشد آنها توسط کاهش دمای ماده با نرخ مشخص کنترل میشود. در نهایت و پس از این مرحله مادهای با شکلپذیری بیشتر و سختی کمتر ایجاد میشود. به طور کلی هر فلزی که برای انجام عملیات حرارتی مناسب باشد برای انجام بازپخت نیز مناسب خواهد بود. در حال حاضر از بازپخت به طور وسیعی در انواع فولاد و چدن، آلومینیوم، مس و برنج استفاده میشود.
معایب و مزایای بازپخت
روش بازپخت دارای مزایا و معایب مختلفی است. از مزایای اصلی این روش میتوان به بهبود خاصیت شکلپذیری، افزایش چقرمگی، کاهش سختی و افزایش خاصیت ماشین کاری فلزات اشاره کرد. به علاوه این روش باعث بهبود هدایت الکتریکی و مغناطیسی درون فلزات میشود. این روش معایبی نیز دارد. یکی از مهمترین معایب این روش زمان گیر بودن آن است.
مزایای سخت کاری فلزات چیست؟
سخت کاری فولاد و به طور کلی فلزات دارای مزایای زیادی است. یکی از مزایای آن این است که از طریق سخت کاری می توان سازه های فولادی اولیه را ساخت. برخی از دیگر مزایا شامل موارد زیر هستند:
- افزایش مقاومت و افزایش طول عمر قطعه
- افزایش مقاومت در برابر ضربههای وارده
- افزایش خاصیت چکش خواری
- ایجاد سهولت در جوشکاری قطعات
- افزایش میزان انعطافپذیری
- بهبود خواص الکتریکی و مغناطیسی
- حذف تنشهای موجود در فلزات
پیشنهاد نویسنده: آبرفت چیست؟
عیوب سخت کاری فلزات چیست؟
با توجه به مزایای زیادی که سخت کاری فلزات میتواند داشته باشد، اما این روشها میتوانند معایبی نیز داشته باشند.
به طور کلی زمانی که مراحل انجام سخت کاری فلزات به درستی طی نشود ممکن است معایب زیر به وجود بیایند.
نرمی
نرم شدن یکی از مشکلاتی است که ممکن است در صورت درست انجام نشدن پروسه سخت کاری برای فلزات ایجاد شود. عوامل زیر میتوانند بر نرمی فلزات تأثیرگذار باشند.
حرارت دهی
اگر در مرحله حرارت دهی دما به میزان کافی بالا نباشد یا مدت زمان اعمال آن کافی نباشد و قطعه پیش از انجام مرحله بعدی بیش از اندازه سرد باشد ممکن است فلز مورد نظر دچار نرمی شود.
کوئنچینگ
عواملی مانند گرم بودن بیش از حد محیط، کوچک بودن محیط، ماده نامناسب، نرخ پایین و کم بودن زمان در این مرحله میتواند باعث نرمی فلزات شوند.
تمپرینگ
بالا بودن بیش از حد دما، تمپرینگ از داخل و نرخ پایین خنککاری در این مرحله میتواند باعث نرمی در فلزات شود.
سختی غیر یکنواخت
یکی از ایرادهایی که میتواند در زمان سخت کاری برای فلزات ایجاد شود، سخت شدن غیر یکنواخت است. این مسأله میتواند تحت تأثیر موارد زیر قرار بگیرد.
حرارت دهی
در این مرحله نامنظم بودن حرارت، ورود سولفور، پوسته پوسته بودن قطعه، چسیبیدن حوضه مذاب و.. میتوانند باعث ایجاد سختی غیر یکنواخت شوند.
کوئنچینگ
در این مرحله کثیف بودن محیط، نزدیکی قطعات به هم، پوشش نامناسب، حرکت نامناسب حبابهای بخار و… میتوانند تأثیرگذار باشند.
تمپرینگ
در این مرحله ایجاد حرارت نامنظم میتواند باعث ایجاد سختی غیر یکنواخت شود.
سختی بیش از حد
سختی بیش از حد نیز میتواند، جزء معایب به حساب بیاید و به شکلهای زیر میتاوند ایجاد شود.
حرارت دهی
دمای سخت کاری بسیار بالا در مرحله حرارت دهی میتواند باعث ایجاد سختی بیش از حد در فلز مورد نظر شود.
کوئنچینگ
نامناسب بودن ماده کوئنچینگ در این مرحله میتواند تأثیرگذار باشد.
تمپرینگ
پایین بودن دمای تمپرینگ نیز میتواند، باعث ایجاد سختی بیش از حد شود.
ترک خوردگی
ترک خوردگی یکی دیگر از مشکلات شایعی است که میتواند، در اثر انجام نادرست سخت کاری فلزات ایجاد شود.
حرارت دهی
مواردی مانند اعمال نامنظم حرارت، عدم پوشش محل پیچ قطعات و عدم اعمال حرارت اولیه میتواند باعث ترک خوردگی فلزات شود.
کوئنچینگ
نگهداری اشتباه درون محیطها و سرد کردن غیر یکنواخت میتواند باعث ایجاد ترک خوردگی در فلزات شود.
سخن نهایی
سخت کاری فلزات یکی از انواع عملیاتهای حرارتی است که به منظور بهبود خواص فلزات از آن استفاده میشود.
در طی سخت کاری به طور کلی سه مرحله حرارت دهی، تثبیت دما و سرددهی باید انجام شود. سخت کاری فلزات دارای روشهای متنوع و بسیار گوناگونی است که بسته به نیاز و خواص مورد نظر که قصد تغییر آنها را داریم این روشها انتخاب میشوند. هر یک از این روشها دارای مراحل مخصوص به خود هستند و خواص مختلفی را نیز تغییر میدهند. همچنین هر کدام از روشهایی که برای سخت کاری فلزات استفاده میشود، دارای مزایا و معایب مخصوص به خود هستند که آنها در بررسی کردیم.