استخراج آهن چگونه انجام میشود؟ روشهای استخراج آهن و مراحل آن
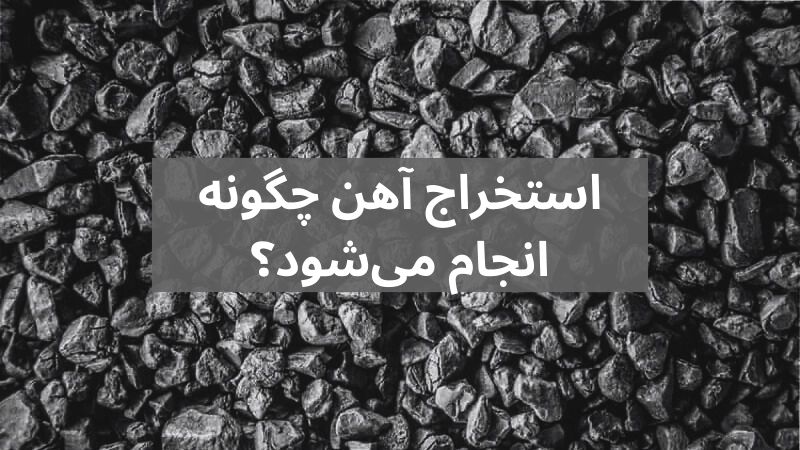
از پیدایش اولیه جوامع بشری تا به الان، همواره بشر به دنبال استخرج مواد اولیه مناسب برای ساخت ابزارآلات و تجهیزات مختلف بوده است. یکی از مهمترینها فلزات و در بین فلزات آهن بوده است. استخراج آهن یکی از مهمترین و اساسیترین فرآیندهای صنعتی است که در طول تاریخ نقش بسزایی در توسعه و پیشرفت جوامع انسانی ایفا کرده است. آهن، بهعنوان یکی از فراوانترین عناصر زمین، در صنایع مختلف از جمله ساختوساز، خودروسازی و تولید ماشینآلات سنگین کاربردهای گستردهای دارد. فرآیند استخراج آهن شامل چندین مرحله تخصصی است که هر یک نیازمند دانش فنی و مهارتهای ویژهای هستند.
ما در این مقاله سعیکردهایم تا تمام مراحل را با تمام جزئیات برایتان شرح دهیم و از شناسایی ذخایر معدنی تا تولید فولاد، تمامی مراحل استخراج آهن را با جزئیات کامل بررسی کنیم تا با فرآیندهای پیشرفته و فناوریهای مدرن این صنعت آشنا شوید.
آهن چگونه بدست میآید؟
سنگهای آهن شامل چندین نوع مختلف هستند که هر کدام دارای ترکیب شیمیایی و ویژگیهای منحصر به فردی هستند.
هماتیت (Hematite)
هماتیت با فرمول شیمیایی Fe2O3Fe2O3 یکی از رایجترین و غنیترین سنگهای آهن است که در بسیاری از معادن جهان یافت میشود. این سنگ معدنی به رنگ قرمز تا قهوهای تیره بوده و حدود 70 درصد آهن خالص دارد. هماتیت بهدلیل فراوانی و غنای بالای آهن، یکی از مهمترین منابع استخراج آهن به شمار میرود. فرآیند استخراج از هماتیت معمولاً شامل خردایش، آسیاب کردن و جداسازی مغناطیسی است.
مگنتیت (Magnetite)
مگنتیت با فرمول شیمیایی Fe3O4Fe3O4 یکی دیگر از سنگهای مهم آهن است که بهدلیل داشتن خاصیت مغناطیسی قوی، بهراحتی قابل شناسایی و جداسازی است. این سنگ معدنی معمولاً به رنگ سیاه تا قهوهای تیره بوده و حدود 72 درصد آهن خالص دارد. فرآوری مگنتیت شامل مراحل خردایش، جداسازی مغناطیسی و گاهی استفاده از تکنیکهای پیشرفتهتری مانند فلوتاسیون است.
سیدریت (Siderite)
سیدریت با فرمول شیمیایی FeCO3FeCO3 یک سنگ آهنی کمتر رایج است که به رنگ زرد تا قهوهای دیده میشود و حدود 48 درصد آهن خالص دارد. استخراج آهن از سیدریت بهدلیل حضور کربنات آهن نیاز به فرآوری پیچیدهتری دارد که شامل حرارت دادن سنگ و جدا کردن دیاکسید کربن است.
لیمونیت (Limonite)
لیمونیت با فرمول کلی FeO(OH)⋅nH2OFeO(OH)⋅nH2O یک سنگ آهن هیدراته است که به رنگ زرد تا قهوهای تیره دیده میشود. این سنگ معدنی معمولاً حدود 60 درصد آهن خالص دارد. لیمونیت بهدلیل محتوای آب و ساختار پیچیده، نیاز به فرآوریهای خاصی دارد که شامل خشک کردن و حرارت دادن است.
روشهای استخراج سنگ آهن
استخراج سنگ آهن یکی از مهمترین فرآیندهای صنعتی است که نیازمند دانش فنی و استفاده از فناوریهای پیشرفته است.
روش استخراج سطحی (Open-Pit Mining)
استخراج سطحی یکی از رایجترین روشهای استخراج سنگ آهن است که در معادنی با ذخایر نزدیک به سطح زمین استفاده میشود. در این روش، لایههای سطحی زمین برداشته میشود تا به سنگ آهن دسترسی پیدا کنیم. مراحل اصلی استخراج سطحی
- برداشت لایههای سطحی: با استفاده از ماشینآلات سنگین نظیر بولدوزر و بیل مکانیکی، لایههای سطحی زمین که شامل خاک و سنگهای غیر معدنی است، برداشته میشود.
- خردایش و بارگیری: پس از دسترسی به سنگ آهن، آن را خرد کرده و به اندازههای کوچکتر تقسیم میکنند تا برای حملونقل مناسب باشد.
- حملونقل: سنگ آهن خرد شده به کارخانههای فرآوری منتقل میشود.
این روش بهدلیل هزینه کمتر و بهرهوری بالاتر در معادن با ذخایر سطحی بسیار محبوب است.
مطلب پیشنهادی: دینامیک خاک چیست؟
روش استخراج زیرزمینی (Underground Mining)
استخراج زیرزمینی زمانی استفاده میشود که ذخایر سنگ آهن در عمق زمین قرار دارند و استخراج سطحی اقتصادی نیست. این روش شامل حفر تونلها و شفتها برای دسترسی به سنگ آهن است. مراحل اصلی استخراج زیرزمینی :
- حفاری شفتها و تونلها: ایجاد شفتها و تونلهایی برای دسترسی به لایههای سنگ آهن.
- استخراج و حملونقل زیرزمینی: سنگ آهن استخراج شده از طریق تونلها به سطح زمین منتقل میشود.
- تهویه و ایمنی: حفظ تهویه مناسب و ایمنی کارگران در معادن زیرزمینی بسیار حیاتی است.
این روش به دلیل هزینه بالاتر و پیچیدگیهای فنی بیشتر، معمولاً در معادن با ذخایر عمیق استفاده میشود.
روش استخراج با انفجار (Blasting)
استفاده از مواد منفجره برای خردایش سنگهای بزرگ و دسترسی به سنگ آهن نیز یکی از روشهای متداول است. در این روش، سوراخهایی در سنگ ایجاد میشود و مواد منفجره در آنها قرار داده میشود. پس از انفجار، سنگهای خرد شده جمعآوری و حملونقل میشوند.
- حفاری سوراخها: سوراخهای مناسب برای قرار دادن مواد منفجره حفر میشوند.
- جایگذاری مواد منفجره: مواد منفجره در سوراخها قرار داده شده و آماده انفجار میشوند.
- انفجار و خردایش: با انفجار کنترلشده، سنگهای بزرگ به قطعات کوچکتر تبدیل میشوند.
مطلب پیشنهادی: ضریب نفوذ پذیری خاک چیست؟
روش استخراج با استفاده از حلالهای شیمیایی (Leaching)
این روش که معمولاً در معادن کمعیار و برای سنگهای خاص استفاده میشود، شامل استفاده از حلالهای شیمیایی برای جدا کردن آهن از سنگ معدن است. محلولهای شیمیایی به داخل سنگ تزریق میشوند و آهن را حل کرده و به سطح زمین میآورند.
- تزریق حلالها: حلالهای شیمیایی به داخل سنگ تزریق میشوند.
- جمعآوری محلول: محلول حاوی آهن به سطح زمین آورده میشود.
- استخراج آهن: آهن از محلول استخراج و خالصسازی میشود.
این روش بهدلیل هزینه بالای مواد شیمیایی و نیاز به تجهیزات ویژه، کمتر مورد استفاده قرار میگیرد.
مراحل استخراج آهن
استخراج آهن از مراحل مختلفی تشکیل شده که هر کدام نقش حیاتی در دستیابی به آهن خالص و قابل استفاده دارند. در این متن به بررسی مراحل مختلف استخراج آهن میپردازیم.
شناسایی و ارزیابی ذخایر معدنی
اولین مرحله در استخراج آهن، شناسایی و ارزیابی ذخایر معدنی است. این مرحله شامل بررسی زمینشناسی و انجام آزمایشهای ژئوفیزیکی و ژئوشیمیایی برای تعیین کمیت و کیفیت ذخایر سنگ آهن است. هدف از این مرحله، تأیید اقتصادی بودن عملیات استخراج است.
آمادهسازی معدن
پس از تأیید ذخایر، مرحله آمادهسازی معدن آغاز میشود.
- پاکسازی و تسطیح زمین: حذف پوشش گیاهی و تسطیح سطح زمین برای ایجاد راههای دسترسی و مکانهای ذخیرهسازی.
- ایجاد زیرساختها: ساخت جادهها، خطوط برق و تأسیسات لازم برای عملیات معدن.
حفاری و انفجار
در این مرحله، حفاری و انفجار برای خرد کردن سنگهای بزرگ به قطعات کوچکتر انجام میشود.
- حفاری سوراخها: ایجاد سوراخهای عمقی در سنگ با استفاده از دریلهای مخصوص.
- جایگذاری مواد منفجره: قرار دادن مواد منفجره در سوراخها.
- انفجار کنترل شده: انجام انفجار برای خردایش سنگها.
بارگیری و حملونقل
پس از انفجار، سنگهای خرد شده بارگیری و به محلهای فرآوری منتقل میشوند.
- بارگیری سنگها: استفاده از ماشینآلات سنگین مانند لودرها و بیلهای مکانیکی برای بارگیری سنگها.
- حملونقل به کارخانههای فرآوری: انتقال سنگها به کارخانههای فرآوری با استفاده از کامیونها و نوار نقالهها.
فرآوری سنگ آهن
در کارخانههای فرآوری، سنگ آهن خرد شده و به مراحل مختلفی برای جداسازی آهن از ناخالصیها وارد میشود.
- خردایش اولیه و ثانویه: کاهش اندازه سنگها با استفاده از سنگشکنها و آسیابها.
- جداسازی مغناطیسی: استفاده از خاصیت مغناطیسی برای جداسازی آهن از سایر مواد معدنی.
- فلوتاسیون: استفاده از مواد شیمیایی برای شناورسازی و جداسازی مواد غیر آهنی.
کنسانترهسازی
در این مرحله، آهن جدا شده به کنسانتره آهن تبدیل میشود.
- خشک کردن و فیلتراسیون: حذف آب از کنسانتره آهن.
- آگلومراسیون: تبدیل کنسانتره به گندله یا کلوخه برای استفاده در کورههای بلند.
کوره بلند (Blast Furnace)
سنگ آهن کنسانترهشده در این مرحله به کوره بلند منتقل میشود. در کوره بلند، سنگ آهن در دمای بالا و در حضور کک (نوعی زغال سنگ) و سنگ آهک ذوب میشود. این فرآیند شامل:
- ذوب آهن: تبدیل سنگ آهن به آهن مذاب.
- حذف ناخالصیها: جدا کردن مواد ناخالص از آهن مذاب.
تولید فولاد
آهن مذاب به واحدهای فولادسازی منتقل میشود، جایی که با اضافه کردن عناصر آلیاژی مانند کربن، کروم و نیکل به فولاد تبدیل میشود.
- دمیدن اکسیژن: حذف کربن اضافی از آهن مذاب.
- اضافه کردن عناصر آلیاژی: افزودن عناصر مختلف برای تولید فولاد با خواص مورد نیاز.
سرند کردن سنگ آهن استخراج شده چگونه انجام می شود؟
سرند کردن سنگ آهن یکی از مراحل اساسی در فرآوری مواد معدنی است که هدف آن جداسازی ذرات بر اساس اندازههای مختلف و حذف ناخالصیها از سنگ آهن استخراج شده است. این فرآیند به بهبود کیفیت سنگ آهن و افزایش بهرهوری در مراحل بعدی کمک میکند.
تعریف سرند کردن
سرند کردن به فرآیند جداسازی ذرات معدنی بر اساس اندازههای مختلف گفته میشود. این فرآیند با استفاده از دستگاههای سرند که دارای شبکهها و توریهای مختلف با ابعاد مشخص هستند، انجام میشود. هدف اصلی سرند کردن، دستیابی به ذرات یکنواخت و جدا کردن ذرات درشت و ناخالصیها از مواد معدنی است.
مطلب پیشنهادی: بتن مسلح چیست؟
مراحل سرند کردن سنگ آهن
- خردایش اولیه: قبل از سرند کردن، سنگ آهن استخراجشده باید به اندازههای کوچکتر خرد شود. این مرحله با استفاده از سنگشکنها و آسیابها انجام میشود. خردایش اولیه کمک میکند تا ذرات بزرگتر به ابعاد قابل مدیریت برای سرند تبدیل شوند.
- انتقال به دستگاه سرند: پس از خردایش اولیه، سنگ آهن خردشده به دستگاههای سرند منتقل میشود. این دستگاهها معمولاً بهصورت لرزشی یا چرخشی عمل میکنند تا مواد معدنی را از طریق توریها عبور دهند.
- جداسازی ذرات بر اساس اندازه: دستگاههای سرند دارای چندین طبقه با توریهای مختلف هستند. ذرات کوچکتر از توری عبور کرده و به طبقات پایینتر منتقل میشوند، در حالی که ذرات بزرگتر در بالای توری باقی میمانند. این جداسازی بر اساس اندازه ذرات، کمک میکند تا مواد معدنی با ابعاد یکنواخت به دست آید.
- حذف ناخالصیها: در حین سرند کردن، ناخالصیهایی نظیر خاک، سنگهای غیر آهنی و مواد زائد از سنگ آهن جدا میشوند. این فرآیند باعث افزایش خلوص و کیفیت سنگ آهن میشود.
- تجمع و حملونقل ذرات سرند شده: پس از جداسازی، ذرات سرندشده به دستههای مختلف جمعآوری میشوند. این دستهها بر اساس اندازه و کیفیت مواد معدنی دستهبندی شده و برای مراحل بعدی فرآوری آماده میشوند.
نتیجهگیری
استخراج آهن یک فرآیند چند مرحلهای و پیچیده است که نقش اساسی در صنایع مختلف ایفا میکند. از شناسایی و ارزیابی ذخایر معدنی تا تولید فولاد نهایی، هر مرحله نیازمند دانش فنی، تجهیزات پیشرفته و مدیریت دقیق است. مراحل اصلی استخراج آهن شامل شناسایی ذخایر، آمادهسازی معدن، حفاری و انفجار، بارگیری و حملونقل، فرآوری سنگ آهن، کنسانترهسازی و تولید فولاد در کوره بلند است.
آشنایی با مراحل و فناوریهای مختلف استخراج آهن برای هر فعال در صنعت معدن و فولاد ضروری است. این دانش به بهینهسازی فرآیندها و ارتقای کیفیت محصولات نهایی کمک میکند و در نهایت باعث توسعه و پیشرفت صنعت و اقتصاد کشور میشود. با توجه به اهمیت بالای این فرآیند، تلاش برای بهبود و نوآوری در استخراج و فرآوری سنگ آهن همواره باید در اولویت قرار گیرد.